Corrugated box manufacturers rely heavily on starch-based adhesives to ensure strong bonding, durability, and overall product quality.
However, when low-grade or improperly formulated adhesives are used, several manufacturing defects and customer complaints arise. Here are some of the most common issues:
1. Poor Bond Strength Leading to Delamination
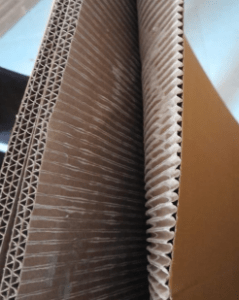
Complaint:
- “The liners are peeling off!”
- “White glue lines after Delamination of liners”
- “After side pasting, flaps get delaminated”
Cause:
- Low-quality starch adhesives lack strong bonding properties, leading to weak adhesion between the liner and flute.
- White lines are caused due to inconsistent gel temperature results in incomplete adhesion during corrugation.
- High water content in low-grade adhesives causes poor fibre penetration.
Impact:
- Box failure compromises structural integrity, risking product damage
Solution:
- Ensure proper viscosity and solid content in adhesive formulation.
- Regularly test adhesive performance using bond strength tests.
- Use MSPL range of caustic-free Corrugation (One Bag Mix) adhesives built to match your machine design and performance.
- Use MSPL formulated adhesives which give 20% higher Compression strength than other counterparts.
2. Increased Drying Time & Production Delays
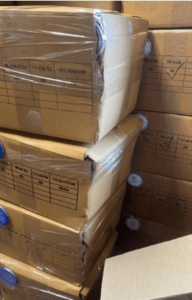
Complaint:
- “The drying process is taking too long!”
- “Our production line is slowing down because the boards are not drying quickly.”
Cause:
- Low-grade starch adhesives have high moisture retention, increasing drying time.
- Poor adhesive formulation leads to improper gelatinization, requiring longer heat exposure.
Impact:
- Lower production efficiency as machines need to run slower which affects the supply chain.
- Higher energy consumption, increasing operational costs.
Solution:
- Use properly processed starch with an optimized gel temperature.
- Use MSPL fast drying adhesives which promotes faster bonding and low moisture in boxes.
3. Mold & Fungal Growth (White Spots on Boxes)
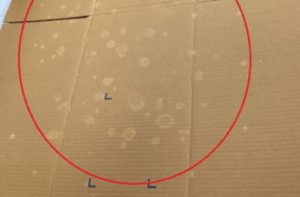
Complaint:
- “Boxes are developing white fungal spots!”
- “Mold is ruining our packaging!”
Cause:
- Low-grade starch adhesives contain impurities and excess moisture, creating an ideal breeding fungus.
- Improper pH balance leads to microbial growth.
- High humidity in storage areas accelerates fungal development.
- Lack of Anti-fungal treatment during paper formation at paper mills.
Impact:
- Health hazards and contamination in food & pharmaceutical packaging.
- Financial losses due to product rejections and wastage stock.
Solution:
- Use paper with Anti-fungal treatment done on it during paper manufacturing.
- Use purified starch adhesives with anti-fungal agents.
- Maintain proper pH control (between 5.5 – 7) to prevent microbial growth.
- Store boxes in dry, well-ventilated areas with humidity control.
- Use our high-quality MSPL NEUTRAL adhesive which achieves 9-10% moisture in boards even in monsoon.
4. Cracking on Creases during Folding
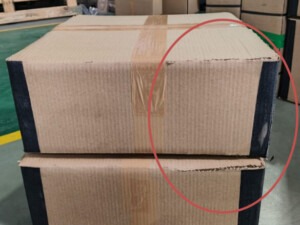
Complaint:
- “Boxes are cracking at the folds!”
- “The fibre is breaking instead of bending properly.”
Cause:
- Excess gum application causes over-hardening of the paper surface.
- Low-quality paper fibres fail to maintain flexibility in boxes.
- Using poor paper quality with lower COBB value in summer season.
Impact:
- Weakened structural integrity, leading to box failure.
- Product returns and complaints from customers.
Solution:
- Optimize adhesive application to avoid overuse.
- Use a balanced starch formulation that provides both bond strength and flexibility.
- Maintain proper moisture levels in the boards by maintaining higher COBB value during summer.
- Use MSPL range of Anti-cracking adhesives which ensures no cracking in boxes even during summers.
5. Flute Marks on Virgin Imported Papers
Complaint:
- “Our premium virgin paper is showing flute marks!”
- “The box appearance is being ruined by the flute impressions.”
Cause:
- Excess gum application leads to softening of liners, making flutes more visible.
- Poor adhesive quality causes uneven bonding, emphasizing flute marks.
- Use of adhesive formulation with pH>9 cause flute marks.
Impact:
- Affects brand image for premium packaging.
- Customers reject boxes for cosmetic defects.
Solution:
- Reduce adhesive viscosity to prevent over-application.
- Adjust machine pressure to avoid excessive compression on virgin papers.
- Use OUR high-quality MSPL NEUTRAL adhesive that promotes even bonding without excess moisture.
6. High Adhesive Consumption & Cost Overruns
Complaint:
- “We are using too much adhesive!”
- “Our costs are rising due to excess starch consumption!”
Cause:
- Low-grade adhesives require higher application volumes to achieve proper bonding.
- Poor adhesive consistency results in overuse during application.
- Weak adhesion leads to rework and wastage, increasing costs.
Impact:
- Increased material costs for starch adhesives.
- Reduced profit margins due to wastage and inefficiencies.
Solution:
- Use high-quality starch adhesives with optimized viscosity and bonding properties.
- Train operators to apply the right amount of adhesive based on board specifications.
- Regularly test adhesive performance to ensure optimal usage.
- We, at MSPL have derived methods which ensure low gum consumption up to 2% of the paper weight which lowers production cost of the final box.
Using low-grade starch-based adhesives in corrugated box manufacturing leads to multiple issues, including delamination, warping, mold growth, cracking, excessive costs, and production delays. These problems not only affect production efficiency but also result in customer dissatisfaction and financial losses.
By investing in high-quality starch adhesives, regularly testing adhesive properties, and optimizing application techniques, manufacturers can significantly improve box performance, reduce wastage, and enhance customer satisfaction.
Why Testing Starch-Based Adhesives matters more than you think!
1. Ensures Bond Quality:
- Proper adhesive properties (viscosity, solids content, gel point) are critical for strong and consistent bonding of liners and flutes.
2. Ensures Low Adhesive Consumption:
- Adequate and correct adhesive application prevents high adhesive consumption.
3. Prevents Production defects like Delamination:
- Inadequate adhesive can lead to weak bonds, causing separation during handling, stacking, or transit.
4. Maintains Machine Efficiency:
- Correct viscosity ensures smooth flow and application, preventing clogging or uneven coating on the corrugator.
5. Optimizes Drying Time and Energy:
- Balanced moisture and solid content levels help achieve optimal drying and requires less energy consumption.
6. Reduces Waste and Downtime:
- Detecting issues early avoids production defects and costly machine stoppages.
7. Improves Box Performance:
- Strong, uniform bonding contributes to better Compression strength, stacking strength and overall box durability.
Essential Testing Equipment’s for Starch-Based Adhesives
To ensure consistent adhesive quality, corrugators must have basic testing equipment. The following are essential testing equipment for evaluating starch-based adhesives:
- B4 cup – Measures the viscosity of the adhesive, ensuring it has the right flow properties.
- Refractometer – Ensures the right ratio of water and starch to optimize bond strength and drying time.
Automatic plants require a more comprehensive set of testing equipment, including tools like moisture meters, infrared thermometers, pin adhesion tester, pH meters, and others to ensure consistent quality and performance. By investing in proper testing equipment and conducting routine checks, corrugators can minimize defects and improve overall production efficiency. Testing is the key for quality boxes.